Special Hybrid Grades
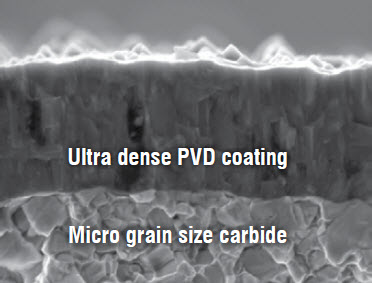
- PVD coating with optimal thermal resistance & added strength
- Tough carbide substrate designed for demanding application
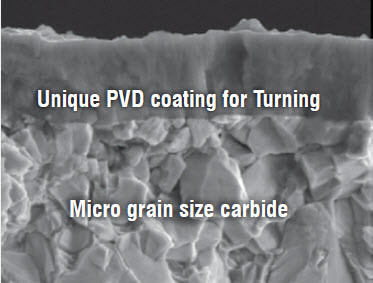
- Substrate and PVD coating designed to balance edge strength & wear resistance
- Excellent cutting performance under harsh machining condition
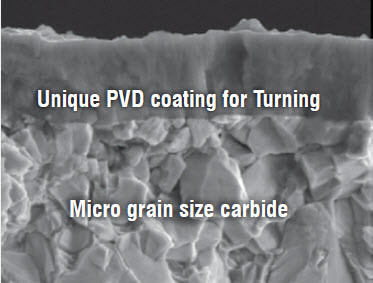
- Thick coating optimized for cast iron applications
- CVD coating with optimal thermal & wear resistance for turning applications
- Exceptional cutting performance attributed to combination of carbide substrate and coating
Damage of Insert & Counter Measure
Description | Solution | |
![]() Rapid Flank Wear |
1. Inappropriate feed(f) rate
2. Cutting speed(s) too high |
1. Adjust feed(f) rate according to depth(ap), width(ae)
2. Reduce cutting speed(s) |
![]() Chipping |
1. Feed(f) rate too high 2. Cutting speed(s) too low 3. Vibration of holder & machine |
1. Reduce feed(f) rate 2. Increase cutting speed(s) 3. Reduce the tool overhang & improve the rigidity of machine and workpiece |
![]() Thermal Crack |
1. Insufficient coolant
2. Cutting speed(s) too high |
1. Check cooling system, supply enough coolant or use dry milling
2. Reduce cutting speed(s) |
![]() Build Up Edge |
1. Cutting speed(s) too low 2. Insufficient coolant 3. Not enough rake angle |
1. Increase cutting speed(s) 2. Supply enough coolant 3. Increase rake angle of change inserts |
![]() Notching |
1. Scaling or work hardening in workpiece surface area
2. Burrs in workpiece |
1. Change/Vary cutting condition (feed & depth) 2. Change path or direction |
![]() Fracture |
1. Wrong insert shape or corner radius
2. Corner radius too small 3. Cutting force fluctuation too high |
1. Choose the insert with bigger corner or radius |
![]() Cratering |
1. Insufficient coolant supply
2. Cutting speed(s) and feed(f) rate too high |
1. Increase coolant supply or concentration 2. Reduce cutting speed(s) and feed(f) rate |
![]() Plastic Deformation |
1. Cutting speed(s) too high
2. Too much stress applied on the cutting edge |
1. Reduce cutting speed(s) 2. Supply enough coolant 3. Choose insert with bigger corner radius |
Technical Formula
Cutting speed (Vc) [m/min.] |
$$Vc={D . π . n }/{1000}$$ [m/min.] |
Revolutions per minute (n) [rev./min.] |
$$n={Vc . 1000 }/{D . π}$$ [rev./min.] |
Feed rate (Vf) [rev./min.] |
$$Vf={fn . n}$$ [rev./min.] |
Feed per tooth [mm/tooth] |
$$fz={Vf}/{n . z}$$ [mm/tooth] |
Metal removal amount [cm3/min.] |
$$Q={ae . ap . Vf}/{1000}$$ [cm3/min.] |
Power consumption [kW] |
$$Pc={Q . kc}/{60 . 102. n}$$ [rev./min.] |
Material designations & dimensions | |
ae | Width of cut [mm] |
ap | Depth of cut [mm] |
D | Cutter diameter [mm] |
Dw | Work piece diameter [mm] |
fz | Feed per tooth [mm/tooth] |
π | Circular constant |
kc | Specific cutting resistance [kgf/mm3] |
n | Revolutions of spindle [min. -1] |
Pc | Power consumption [kW] |
Q | Metal removal amount [cm3/min.] |
Vc | Cutting speed [m/min.] |
Vf | Feed rate [mm/min.] |
fn | Feed per revolution [mm/rev.] |
z | Effective number of edges [pcs.] |
n | Mechanical efficiency [%] |
Trouble Shooting
Trouble | Cause | Counter measure | |||
Cutting conditions | |||||
Cutting speed | Feed rate | Depth of cut | Coolant | ||
Heat | Inappropriate cutting condition |
↓ | ↓ | ↓ | |
Poor surface quality of machined surface |
Premature insert wear |
↓ | ● | ||
Chipping of cutting edge |
↓ | ↓ | |||
Built up edge | ↑ | ↑ | ● | ||
Inappropriate cutting condition |
↑ | ↓ | ↓ | ● | |
Chatter | ↓ | ↓ | ↓ | ● | |
Change of cutting edge line |
Inappropriate cutting condition |
↓ | ↑ | ||
Burr, Chipping (Steel, Aluminum) |
Inappropriate cutting condition |
↓ | ↑ | ● | |
Chipping of workpiece (Cast Iron) |
Inappropriate cutting condition |
↓ | ↓ | ||
Burr (Mild steel) |
Inappropriate cutting condition |
↑ | ![]() |
● |
- ↓ : decrease ↑ : increase : depends on status ● : use coolant
Universal Grades Recommend Cutting Conditions : PVD coating for MILLING and DRILLING Application
ISO | Material Group | VDI Group | Relative
materials (DIN) |
Hardness
HB |
Cutting speed
(m/min.) |
P |
Non-alloy steel | 1 - 5 | 9 SMn 28, C35,
C50, C40E, C45E, 49 CrMo 4 |
125 - 250 | 150 - 250 |
Low alloy steel | 6 - 9 | 13 CrMo 44,
40NiCrM022, 58 CrV 4 |
200 - 350 | 140 - 200 | |
High alloy steel | 10 - 11 | X 40 CrMoV 5 1,
X100 CrMoV 5 1, S6-5-5 |
200 - 325 | 80 - 140 | |
M |
Ferritic/martensitic
Stainless steel |
12 - 13 | X6Cr13,
X10CrA118, X20CrNi175 |
200 - 240 | 130 - 190 |
Austenitic | 14 | X5 CrNi 18 9,
X5 CrNiMo 17 13 3, X6 CrNiTi 18 9 |
180 | 100 -200 | |
K |
Grey cast iron | 15 - 16 | GG15, GG20,
GGG40, GG-35 |
180 - 260 | 160 - 200 |
Malleable castiron | 19 - 20 | GTS-35-10, GTS-35,
GTS70-02, 20mN5 |
130 - 230 | 130 - 180 | |
S |
Fe, Ni or Co based | 31 - 35 | X12 NICrAlTi 31 20,
TiAl5Sn2 |
200 - 350 | 30 - 50 |
Titanium and
Ti-alloy based |
36 - 37 | TiCu2, TiAl6V4,
TiAl6V4ELI |
- | 35 - 75 | |
H |
Hardended steel | 38 - 39 | C 105 W1,
75 CrMoNiW 6 7 |
55 - 60 HRc | 55 - 65 |
Chilled Cast iron | 40 | G-X 260 NiCr 4 2,
X15 CrNiSi 25 20 |
400 | 45 - 55 | |
Cast iron | 41 | G-X 300 CrMo 15 3 | 55 HRc | 55 - 65 |
- Above recommend cutting condition can be changed according to the customer’s machining condition.
Universal Grades Comparison Chart : PVD MILLING and DRILLING
ISO | Symbol | BlueCut | Sandvik | Kennametal | Seco | Iscar | Mitsubishi | Sumitimo | Tungaloy | Taegutec |
P |
P10 | YB602 | GC1010 GC1025 |
KC715M | IC250 IC808 IC908 |
ACP200 | TT2510 TT7080 |
|||
P20 | YB602 | GC1010 GC1025 GC2030 |
KC522M KC525M |
F25M MP3000 |
IC250 IC808 IC908 IC928 |
MP6120 VP15TF |
ACP200 | AH725 AH120 AH330 GH330 |
TT2510 TT7080 TT9080 |
|
P30 | YB602* | GC1010 GC1030 GC2030 |
KC725M KC530M |
F25M MP3000 F30M |
IC250 IC808 IC908 IC928 |
MP6120 VP15TF MP6130 VP30RT |
ACP200 ACP300 |
AH725 AH120 AH130 GH130 |
TT8080 TT9080 |
|
P40 | YB602* | GC1030 | KC735M | F40M T60M |
VP30RT | ACP300 | AH140 | TT8080 TT9080 |
||
M |
M10 | YB602* | GC1025 GC1030 |
KC715M | IC903 | |||||
M20 | YB602* | GC1025 GC1030 GC1040 GC2030 |
KC730 KC522M KC525M |
F25M MP3000 |
IC250 IC300 IC808 IC928 |
VP15TF MP7130 MP7030 VP20RT |
ACP200 | AH725 AH120 AH330 GH330 |
TT9080 | |
M30 | YB602 | GC1040 GC2030 |
KC725M KC735M |
F30M F40M MP3000 |
IC250 IC300 IC808 IC928 |
VP15TF MP7130 MP7030 VP20RT |
ACP200 ACP300 |
AH120 AH725 GH130 GH340 |
TT8080 TT9080 |
|
M40 | YB602 | F40M | MP7140 VP30RT |
ACP300 | AH140 | TT8080 TT9080 |
||||
K |
K10 | YB602 | GC1010 | KC510M | IC350 IC810 IC900 IC910 IC950 |
MP8010 | AH110 GH110 AH330 |
TT6080 TT7080 |
||
K20 | YB602* | GC1010 GC1020 |
KC520M KC525M |
MK2000 | IC350 IC830 IC928 |
VP15TF VP20RT |
ACK300 | GH130 | TT6080 TT7080 |
|
K30 | YB602* | GC1020 | KC725M KC735M |
IC350 IC830 IC928 |
VP15TF VP20RT |
ACK300 | AH725 AH120 AH130 GH130 |
|||
S |
S10 | YB602* | GC1025 | KC510M | IC903 | MP9120 VP15TF |
||||
S20 | YB602* | GC1025 GC2030 |
KC522M KC525M |
IC300 IC808 IC908 IC328 |
MP9120 VP15TF MP9130 MP9030 |
TT9080 | ||||
S30 | YB602 | GC2030 | KC725M | F40M | IC830 IC928 |
TT8080 TT9080 |
||||
H |
H10 | YB602 | GC1010 GC1030 |
KC635M | MH1000 F15M |
IC900 | VP15TF VP10H |
TT2510 TT6080 |
||
H20 | YB602 | GC1010 GC1030 |
KC635M | F15M | IC900 IC808 IC908 |
VP15TF | TT2510 TT6080 |
|||
H30 | YB602 | KC530M | MP3000 F30M |
IC808 IC908 IC1008 |
Universal Grades Comparison Chart : PVD MILLING and DRILLING
Universal Grades Comparison Chart : TURNING
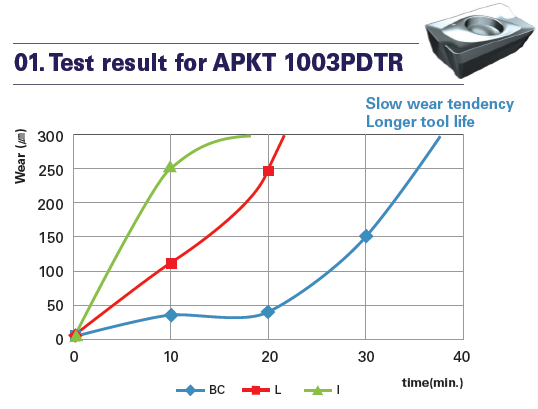
Test Condition
Material (Alloy tool steel) |
DIN : X100CrMoV5 1 AISI : D2 JIS : SKD11 |
Workpiece HB | 210 ~ 220 |
Workpiece size | 150 x 200 x 120 |
Vc(m/min.) | 140 |
fz(mm/tooth) | 0.1 |
ap/ae(mm) | 8 / 3 |
Coolant | Dry |
*Test finishing wear value : 300㎛(flank wear)
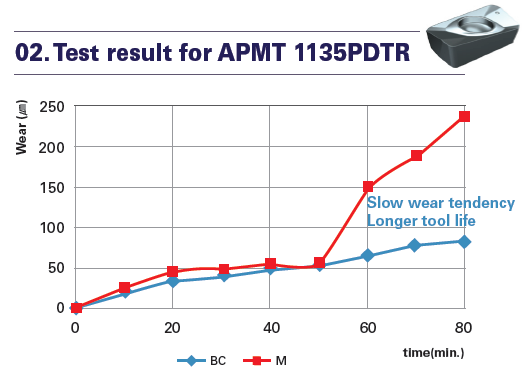
Test Condition
Material (Alloy steel) |
DIN : 42CrMo4 AISI : 4140 JIS : SCM440 |
Workpiece HB | 190 ~ 200 |
Workpiece size | 300 x 60 x 150 |
Vc(m/min.) | 180 |
fz(mm/tooth) | 0.15 |
ap/ae(mm) | 2 / 20 |
Coolant | Dry |
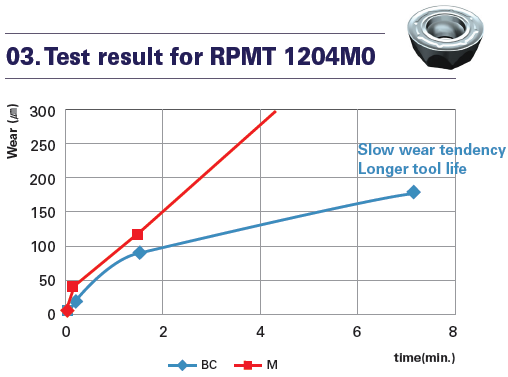
Test Condition
Material (Alloy tool steel) |
DIN : X100CrMoV5 1 AISI : D2 JIS : SKD11 |
Workpiece HB | 210 ~ 230 |
Workpiece size | 120 x 100 x 150 |
Vc(m/min.) | 120 |
fz(mm/tooth) | 0.23 |
ap/ae(mm) | 1.5 / 20 |
Coolant | Dry |